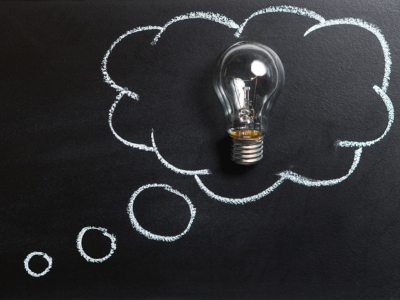
Introduction to Learn
Learning Objective: To gain a basic understanding of what lean is and how applying lean methods can improve the functioning of your practice.
What is Lean?
Lean methods in healthcare aim to minimise waste that does not create value for patients. Lean recognises that patients are the end consumers of care, and that value for practices is best created by creating value for patients.
Why implement Lean?
Improving patients’ experience of the practice improves staff experience and business sustainability.
By using lean methods, all staff feel empowered to identify areas of waste and eliminate any steps in a process that do not add value to patients or increase the operational efficiency of the practice. The time taken to improve processes is typically repaid by these improvements.
Staff working in practices that use lean methods report being happier and more satisfied with their work. They usually know what can be improved; practice leaders need to support staff to make these changes.
Lean methods aim to reduce the 8 wastes detailed below.
Waste |
Description |
Example |
Transportation |
Unnecessary movement of supplies/equipment relating to work being done. |
Hard copy files being sent around a practice. |
Inventory |
”Work in process” beyond what is required to serve the customer. |
Cabinets full of files. |
Motion |
Unnecessary movement of people doing the work. |
Retrieving documents from multiple file boxes. |
Underutilisation |
Instances in which available workplace resources are not fully leveraged to produce and deliver services. |
Underutilised: - Office space - Technology - Data |
Waiting |
Delays between one process step ending and the next beginning. |
Patient waiting to be seen by clinician. |
Over-processing |
Adding value to a service beyond what customers want or will pay for |
Generating reports that no one reads. |
Over-production |
Producing outputs beyond what is needed for immediate use. |
Printing and filing patient information that is not required. |
Defects/Re-work |
Any aspect of the service that compromises quality in the eyes of the customer. |
Billing errors. |
Who does what?
Staff |
Role |
Owners/Governance |
Support a lean practice culture. Assure staff that lean is good for patients and them. |
Receptionists/Administrators |
Identify processes which can be improved upon in your daily work. Participate in work to improve these processes. |
Nurses |
Identify processes which can be improved upon in your daily work. Participate in work to improve these processes. |
General Practitioners |
Identify processes which can be improved upon in your daily work. Participate in work to improve these processes. |
Management |
Create an awareness of lean. Support all staff to improve current processes. Measure and evaluate lean work. |
WellSouth |
Support everyone in the practice to learn about lean methods and how to apply these to their own areas of work. |
Measurements
It is important to measure before and after change to ensure the changes implemented are having the desired effect. The measures chosen will depend on which waste you are trying to reduce and the situation in your practice. A Plan Do Study Act (PDSA) cycle a useful tool for measuring change.
An important element in lean initiatives is to understand where work is best done. It may be that asking a person to do an additional task saves another person more time. Working as a team is key.
Patients
If any changes you are planning to make will affect how patients interact with the practice then it is important they understand this. Some effective ways to communicate this to the patient include using patient portal, social media, telephone message, email, text, and posters.
For particularly important changes, the most effective way of communicating is for key staff to tell patients when they see them.
Consider the equity implications for communicating with patients – you might need to go the extra mile to get the message across.
Helpful Tips
Small changes can make a big difference to how patients and staff interact with the practice. Ask staff what tasks they find laborious and work to improve them, no matter how small.
Standardising clinic rooms so that anyone who uses the space knows exactly where everything is stored is an excellent lean process. It may be hard to pry personal belongings away from certain people, but it can make a big difference to the efficiency of your practice.
Space is a valuable resource in a practice. Storing boxes of files may not be the most effective use of that space. See if you can downsize and send the remainder to storage, utilising that space more effectively, even opening a new clinic room or using it for a Health Improvement Practitioner (HIP).